We want to talk again about heat pumps on the wave of a very complete and interesting white paper made by Thomas Nowak, Secretary General of the European Heat Pump Association (EHPA). The document develops in depth the full potential of heat pumps technology for decarbonization and the deployment of renewable energy. Let’s thus introduce the theme of Renewables, which will be the special focus of our Tempco Blog through the entire month of February 2023.
Heat pumps are machines able to supply both heating and cooling as well to produce hot water for residential, commercial and industrial applications. The paper (based on 2015 data but still gives a valid idea) estimates that 50,3% of energy demand in Europe is related to heating and cooling applications. In particular, energy demand for space heating and process industry heating accounts for 85% of the overall demand. And it is mainly fulfilled by fuel sources, gas in first place.
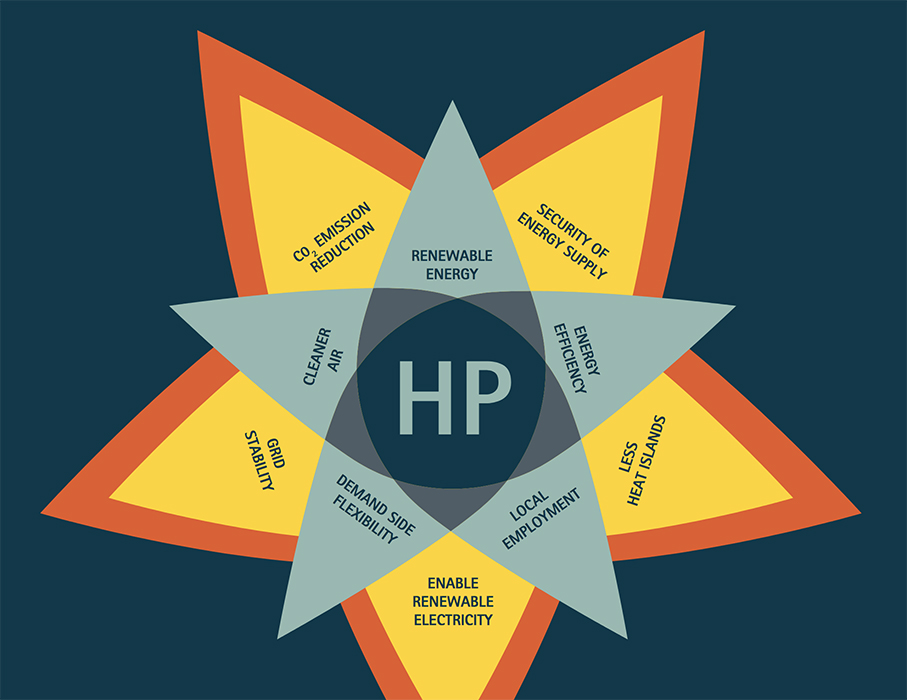
The working principle of a heat pump is a thermodynamic cycle powered by electric energy which allows to provide heating and cooling in parallel. Most part of heat pump technologies are based on a electric gas compression cycle. In case the electric energy that powers the compression cycle in sourced by renewables, the heat pump technology becomes totally green and 100% sustainable. The sustainability can even be pushed further with the substitution of traditional refrigerants and technical gas, high GWP and polluting, with new gases with low GWP, such as CO2 (R744) which is already employed in innovative CO2 refrigerating groups.
The basis of the compression cycle in a heat pump is the classic and already well known, but let’s summarize it: it consists of 5 components, an evaporator, which is a liquid to gas heat exchanger, a compressor, a condenser, I.e. a gas to liquid heat exchanger, an expansion valve and a transfer fluid (the refrigerant).
A heat pump, in order to achieve heating or cooling, can then employ renewable energy coming from air, water or ground (geothermal energy), as explained at pages 21-22, to realize applications such as those developed by Tempco at the Marina di Loano seaport and using immersion exchangers on the Como Lake.
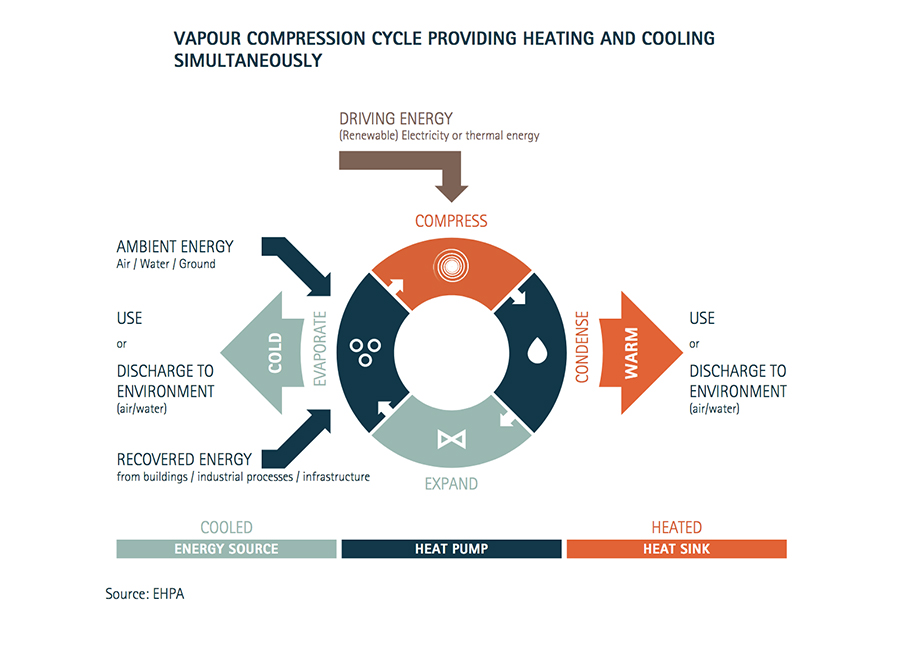
The white paper also offers an interesting estimate of the energy balance of a heat pump: typical heat pumps require indeed one unit of electricity – mostly required to power the compression cycle – in addition to 2-4 units of renewable energy or waste energy coming from another process, to provide 3-5 units of heat output and 2-4 units of cooling. With the further development of the related technology, heat pumps energy efficiency will even further increase. The majority of heat pumps applications can provide heating at 30-55° C, and hot water at 55° C to 65° C. The latter can be increased by deploying CO2 heat pumps, which in addition of being an alternative gas to traditional refrigerants will also increase the overall efficiency of heat pumps. The future challenge is then, in CO2 heat pumps and as well as for CO2 refrigeration, to design and develop special components able to withstand the high temperatures and high pressures involved with CO2 applications.
Finally, is also very appealing the prospect on the feasibility of a future configuration of heat pumps combined with a thermal storage tank and a battery, that will allow heat pump based systems to normalize the demand curve on power grids by providing load shaping and load shifting services, thus making smart grids more flexible, reliable and stable and at the same time increasing the level of independency of heat pumps.
Stay updated on the latest applications of thermal energy management by subscribing our monthly Tempco Newsletter – Solid Temperature.