Nel progettare una macchina termica, scambiatori di calore, unità di termoregolazione e torri evaporative, sistemi di pompaggio, tubazioni per trasmissione di fluidi e quant’altro, sono molti i fattori da valutare, dalla compatibilità dei materiali di costruzione al dimensionamento dei componenti in relazione alle caratteristiche dei fluidi coinvolti, fluidi di lavoro e sostanze impiegate nel processo produttivo con cui i macchinari sono a continuo contatto.
Il sito Tempco alla sezione Risorse offre in download una nutrita serie di materiali tecnici, tabelle e datasheet, un prezioso aiuto per la corretta valutazione progettuale di un impianto per gestione dell’energia termica.
Partiamo con la Compatibilità chimica di alcuni materiali plastici e metallici, impiegati per componenti quali dispositivi di pompaggio, piastre, valvole, tubazioni e guarnizioni, che trovate al link sottostante.
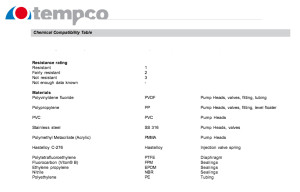
http://www.tempco.it/wp-content/uploads/2012/12/Chemical_compatibility.pdf
La tabella fornisce una guida iniziale, basata sulle indicazioni fornite dai costruttori unite all’esperienza maturata in Tempco, tenendo poi presente che la resistenza chimica dei materiali dipende da una varietà di fattori presenti nei singoli contesti applicativi, e che vanno pertanto valutati con attenzione caso per caso.
Qui invece la resistenza chimica di Rame e Acciaio Inox AISI 316 all’acqua in ragione di parametri quali la presenza di alcune sostanze in soluzione o della conduttività elettrica.
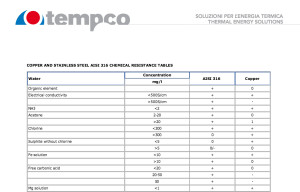
http://www.tempco.it/wp-content/uploads/2012/12/aisi316.pdf
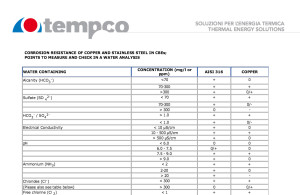
http://www.tempco.it/wp-content/uploads/2012/12/CBE_corrosion_resistance.pdf