Visitors to the fourth edition of Hydrogen Expo, in Piacenza from 21 to 23 May 2025, will be able to see firsthand the technological developments that all major suppliers of components and systems are developing for the hydrogen economy. Hydrogen is a key resource for decarbonisation and the transition to a more efficient and sustainable green industry.
Electrolysers, fuel cells and hydrogen refueling stations impose very challenging requirements, new and special for the industrial sector, which depending on the operating principle of the different technologies may involve resistance to very high pressures, high temperatures and compatibility of the materials used with corrosive fluids.
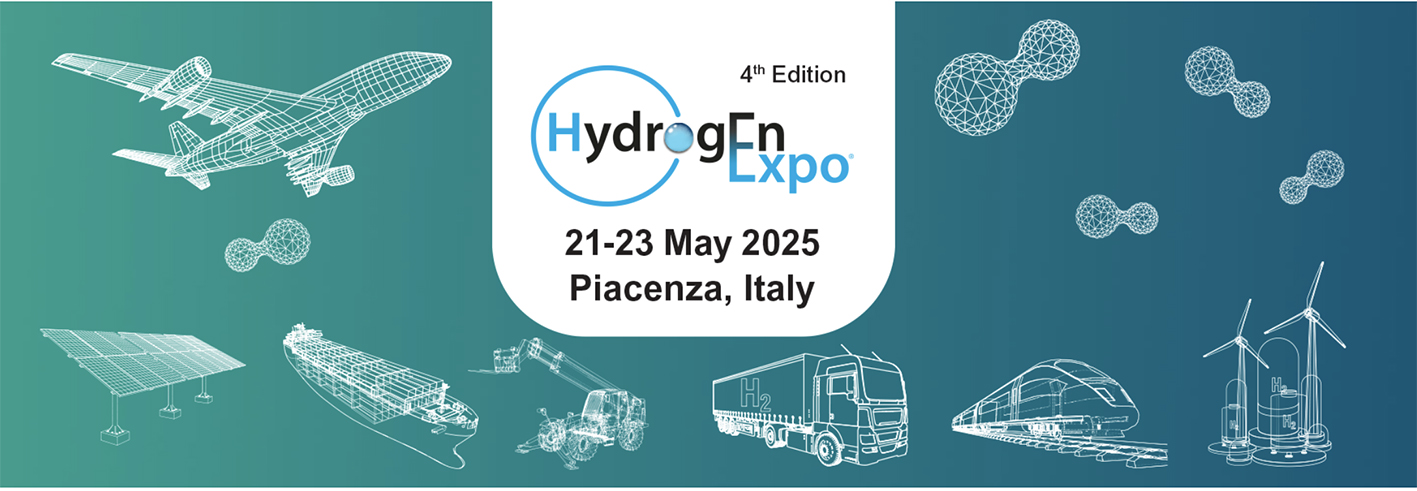
The hydrogen molecule in particular is very small, posing an unprecedented challenge to the sealing technologies and components of systems. Several companies have developed specific technologies for hydrogen technologies in their range of solutions. For example, Parker Hannifin has developed a range of sealing solutions designed to meet the special requirements of hydrogen electrolysers and fuel cells, in particular for the reliable sealing of bipolar plates, essential components of the units responsible for the chemical reaction. Here the bipolar plates act as connecting elements between the individual cells, not only to distribute and cool the unit, but also to seal it and protect it from the external environment.
Henkel, a well-known manufacturer of industrial adhesives, has also recently launched a new range of sealing fittings, specifically designed and optimized for the sealing of threaded fittings for hydrogen, able to guarantee the safety requirements and outstanding performance in critical environments such as hydrogen systems.
A range of innovative technologies and solutions that promote the development and expansion of the hydrogen economy, ensuring efficiency, operational reliability of systems throughout the supply chain, including production, distribution, storage and use of hydrogen. The latest innovations for the hydrogen industry will therefore be the focus of to the May appointment with Hydrogen Expo in Piacenza, an event in which Microchannel Devices, Tempco’s partner for PCHE heat exchangers technology, will also participate, showing the advantages of these exhangers for hydrogen applications at the company’s stand on Pad 1, B118.
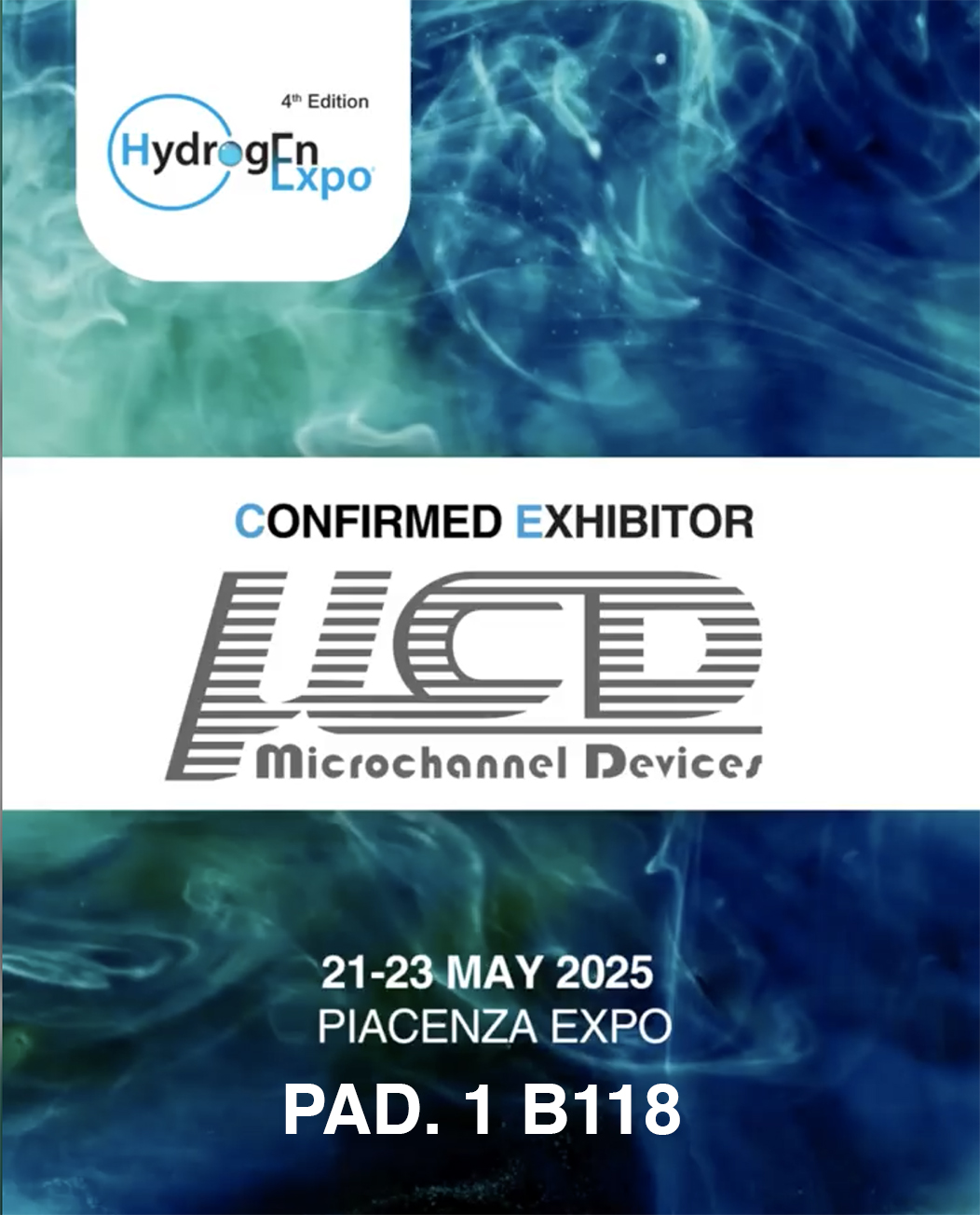
Tempco offers various specific plate heat exchangers solutions for hydrogen applications, both in the process area, with special brazed plate exchangers that can withstand operating pressures of up to 140 bar – also used for CO2 -; and in the distribution of hydrogen with the innovative PCHE exchangers, obtained by diffusion bonding technology and photoetching of the plates.
These special production techniques employed for printed circuit heat exchangers allow, in particular, to obtain a monolithic heat transfer pack with very high mechanical resistance and to realize customizable layouts of the thermal transfer microcircuits. This allows for the creation of PCHE even in multistream mode, ideal for cooling different gas streams in multi-stage compressors typically used at hydrogen fuelling stations.